The Rise of Automotive Plastic Parts: Innovations in the Metal Fabrication Industry
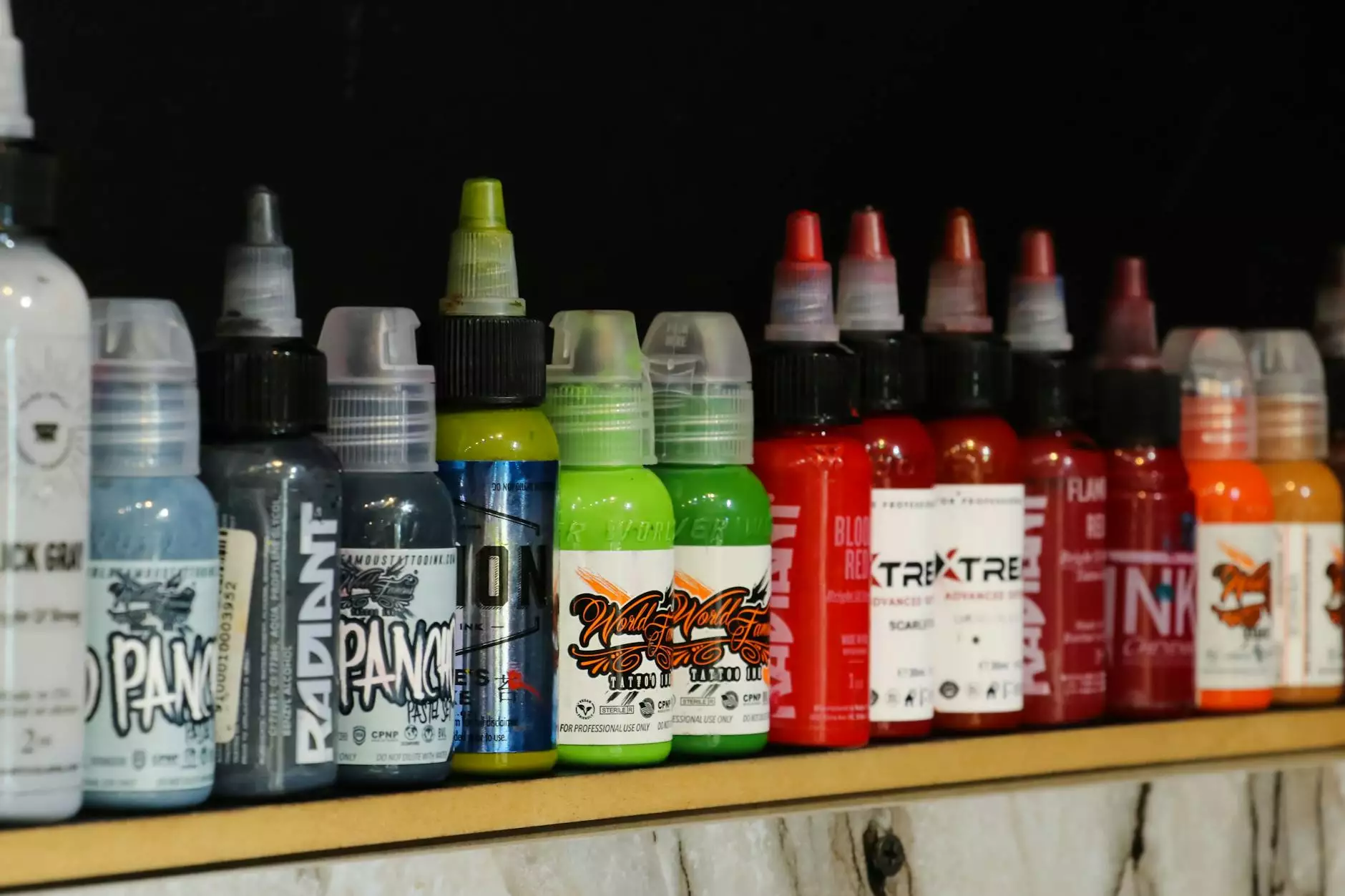
In the ever-evolving world of the automotive industry, automotive plastic parts have emerged as a pivotal component that drives innovation, efficiency, and sustainability. As manufacturers strive to meet the demands of modern consumers and regulatory standards, the shift towards plastic components has profound implications. At the forefront of this evolution are companies like DeepMould that specialize in metal fabrication while also embracing the advantages of utilizing plastic parts.
Understanding Automotive Plastic Parts
Automotive plastic parts refer to components used in vehicles that are produced from various types of plastics. These parts are integral to a vehicle's functionality, aesthetics, and overall performance. From exterior elements like bumpers to interior components such as dashboards and trim, plastics have become indispensable.
The Advantages of Using Plastics in Automotive Manufacturing
The integration of plastics into automotive design and manufacturing comes with numerous benefits:
- Weight Reduction: One of the primary advantages of plastic parts is their lightweight nature, which contributes to improved fuel efficiency and reduced emissions.
- Cost-Effectiveness: The manufacturing processes for plastic parts, including injection molding, can be more affordable compared to traditional materials, reducing overall production costs.
- Design Flexibility: Plastics offer greater freedom in design, allowing for more intricate shapes and features that can enhance aesthetic appeal.
- Corrosion Resistance: Unlike metals, plastics do not rust, which can prolong the life of automotive parts exposed to the elements.
- Noise Reduction: Plastics can absorb sound, contributing to a quieter and more comfortable ride.
The Role of Metal Fabricators in Producing Automotive Plastic Parts
Metal fabricators like DeepMould play a critical role in the production and integration of automotive plastic parts. While primarily focused on metals, these companies have adapted their processes to accommodate the rise of plastic components in vehicles.
1. Advanced Manufacturing Techniques
To optimally fabricate both metal and plastic components, metal fabricators employ various advanced manufacturing techniques:
- CNC Machining: Computer Numerical Control (CNC) machining is essential for creating precise metal parts that work in conjunction with plastic components.
- Injection Molding: This technique is specifically suited for mass-producing complex plastic parts efficiently.
- 3D Printing: Emerging technologies, such as additive manufacturing, allow for rapid prototyping of plastic parts, enabling quicker iteration and innovation.
2. Collaboration with Automotive Manufacturers
Effective collaboration between metal fabricators and automotive manufacturers is crucial. This synergy ensures that automotive plastic parts meet stringent quality standards while optimizing performance.
Environmental Considerations and Sustainability
The automotive industry is under increasing pressure to enhance sustainability efforts. The use of automotive plastic parts plays a significant role in this initiative:
- Recyclability: Many automotive plastics can be recycled, which decreases waste and promotes circular economy principles.
- Energy Efficiency: Lightweight plastic parts contribute to energy savings in the manufacturing process and vehicle operation.
- Emphasis on Bio-Based Plastics: The industry is exploring the use of bioplastics derived from renewable resources to alleviate the environmental impacts of petroleum-based products.
Future Trends in Automotive Plastic Parts
As the automotive landscape continues to evolve, several trends are shaping the future of automotive plastic parts:
1. Increased Use of Advanced Composites
The shift towards more advanced composite materials, which combine plastics with fibers like carbon or glass, promises enhanced strength while maintaining lightweight properties.
2. Smart Plastics
Integration of smart technologies into plastics, such as sensors and conductivity, will enable real-time monitoring of vehicle performance and condition.
3. Greater Customization
With advancements in 3D printing technology, manufacturers can offer greater customization options for automotive plastic parts, tailoring components to specific vehicle models and consumer preferences.
DeepMould: Leading the Charge in Innovation
As a prominent player in the metal fabrication industry, DeepMould stands out for its commitment to innovation. By embracing the integration of automotive plastic parts into their repertoire, they showcase versatility and forward-thinking. Their experience in metal fabrication provides a strong foundation for developing hybrid components that leverage the strengths of both metals and plastics.
Conclusion: The Bright Future of Automotive Plastic Parts
In conclusion, the transition toward automotive plastic parts within the automotive industry signifies a major step toward modernized manufacturing practices. Companies like DeepMould are crucial in shaping this future through advanced fabrication methods and strategic collaborations. As the industry embraces sustainability and innovation, the potential for automotive plastic parts is limitless, setting the stage for a new era in vehicle design and manufacturing.
FAQs About Automotive Plastic Parts
What materials are commonly used for automotive plastic parts?
Common materials include polypropylene (PP), polycarbonate (PC), acrylonitrile butadiene styrene (ABS), and nylon (PA). Each material has properties that make it suitable for specific applications within automotive manufacturing.
How does the weight of plastic parts impact vehicle performance?
A reduction in weight from using automotive plastic parts leads to improved fuel efficiency and better handling performance due to reduced overall vehicle mass.
Are automotive plastics recyclable?
Yes, many automotive plastics can be recycled, and manufacturers are increasingly looking for ways to integrate recycled materials into their production processes.