The Essential Role of Die Casting Parts Manufacturers in Today's Manufacturing Landscape
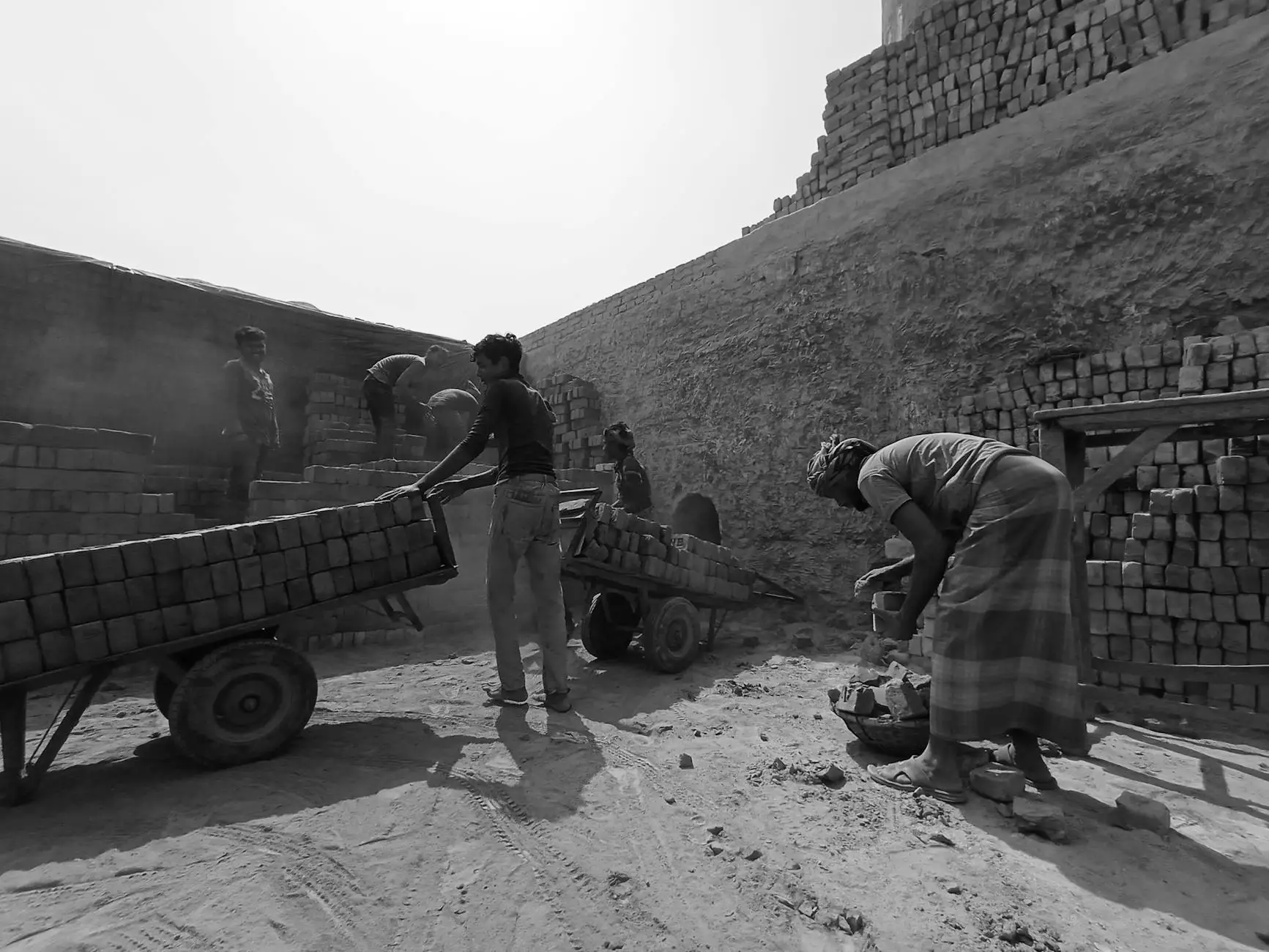
The world of manufacturing is continuously evolving, integrating advanced technologies and innovative processes to meet the demands of various industries. One of the crucial aspects of this evolution is die casting, a manufacturing process that enables the production of complex and high-precision metal parts. Die casting parts manufacturers play a significant role in this process, making them integral to the modern manufacturing ecosystem.
Understanding Die Casting
Die casting is a metal casting process that involves forcing molten metal under high pressure into a mold cavity. This technique produces intricate shapes and can be utilized with various metals, including aluminum, zinc, and magnesium. The precision and efficiency of die casting make it a preferred method in numerous sectors.
Key Advantages of Die Casting
- High Precision and Reproducibility: Die casting allows for tight tolerances, ensuring that parts are produced with remarkable consistency.
- Complex Geometries: Manufacturers can create complex shapes that would be impossible or cost-prohibitive with other methods.
- Durability: Parts produced through die casting have excellent mechanical properties and can withstand demanding applications.
- Cost-Effectiveness: Although initial tooling costs can be high, the long-term production costs are often lower due to the efficiency and speed of the die casting process.
The Role of Die Casting Parts Manufacturers
Die casting parts manufacturers are the backbone of this process, providing essential expertise, resources, and technologies. They are responsible for designing, engineering, and producing die cast parts that meet specific requirements of their clients. Here are some key responsibilities of these manufacturers:
1. Design and Engineering
Transforming concepts into reality starts with effective design and engineering. Die casting parts manufacturers utilize advanced software, such as CAD (Computer-Aided Design), to create accurate models of the desired parts. This stage is crucial, as it ensures that the final products meet the necessary specifications and perform optimally in their application.
2. Tooling
Once the design phase is complete, die casting parts manufacturers develop molds or dies, a critical step in the die casting process. High-quality tools are essential for producing precise components. Manufacturers often invest in advanced machining technologies and meticulous craftsmanship to create durable and efficient tooling that can withstand the rigors of high-pressure casting.
3. Production and Quality Control
With tooling in place, production can commence. Manufacturers utilize automated systems and state-of-the-art die casting machines to ensure efficiency and precision. Throughout this stage, rigorous quality control measures are implemented. This includes inspections for defects, measurements for tolerances, and tests for mechanical properties. Ensuring the quality of each part not only satisfies client requirements but also upholds the manufacturer's reputation.
4. Materials and Finishing
The choice of material significantly impacts the performance of die cast parts. Die casting parts manufacturers often offer a range of materials tailored to meet specific strength, weight, and corrosion resistance requirements. Moreover, manufacturers may finish parts with coatings, polishing, or surface treatments to enhance aesthetics and functionality.
Industries Benefiting from Die Casting Parts Manufacturing
Die casting is not confined to a single industry; it transcends various sectors, each reaping the benefits of this remarkable process. Here are some industries where die cast parts are pivotal:
1. Automotive Industry
The automotive industry is one of the largest consumers of die casting parts. Components such as engine blocks, transmission housings, and structural components are produced using die casting due to their strength and weight advantages. Manufacturers work closely with automotive companies to develop specialized parts that enhance performance and improve fuel efficiency.
2. Aerospace and Defense
In the aerospace sector, die cast parts are essential for producing complex components that meet rigorous safety and performance standards. From turbine components to housing for avionics systems, the precision of die casting ensures reliability under extreme conditions.
3. Electronics
The electronics industry relies on die casting for parts like housings and heat sinks. These components must not only be precisely manufactured but also efficient in thermal management. The ability to produce intricate features through die casting makes it a go-to for electronics manufacturers.
4. Consumer Goods
Die casting is also prevalent in the manufacturing of consumer goods. Products ranging from hardware components to appliances benefit from the durability and design flexibility offered by die casting.
5. Medical Devices
In the medical field, where precision is paramount, die casting plays a crucial role in fabricating components for devices and surgical instruments. Manufacturers must adhere to strict regulatory standards to ensure that parts are safe and effective for use in medical applications.
Choosing the Right Die Casting Parts Manufacturer
When selecting a die casting parts manufacturer, several factors must be taken into consideration to ensure that you partner with a capable provider:
1. Experience and Expertise
Look for manufacturers with extensive experience in the die casting industry. Their expertise will play a critical role in navigating challenges and optimizing the production process.
2. Technology and Capabilities
Examine the manufacturer’s technology and machinery. The latest die casting machines can produce higher quality components faster and more efficiently.
3. Quality Certifications
Manufacturers that hold quality certifications, such as ISO, demonstrate their commitment to producing parts that meet or exceed industry standards.
4. Customer Support
Solid communication and support throughout the production process are essential. A good manufacturer should provide updates, respond to inquiries, and collaborate closely with clients to achieve the desired results.
Future Trends in Die Casting
The die casting industry is poised for growth, with several trends shaping its future:
1. Automation and Smart Manufacturing
The integration of automation technologies and the Internet of Things (IoT) is revolutionizing the die casting process. Automated systems are enhancing efficiency, reducing production times, and minimizing human error.
2. Sustainability Practices
As industries move towards greener practices, die casting parts manufacturers are adopting sustainable methods. This includes recycling scrap materials and optimizing energy usage during production.
3. Lightweighting Movement
With the growing demand for lighter components, especially in automotive and aerospace applications, die casting manufacturers are innovating to create lighter but equally strong parts.
4. Advanced Materials
The exploration of new alloys and materials is opening doors to new applications where die casting can be utilized, extending its versatility within various industries.
Conclusion
Die casting parts manufacturers are vital contributors to modern manufacturing, providing the precision and efficiency that various industries demand. Understanding the die casting process, selecting the right manufacturer, and keeping up with industry trends can significantly enhance product quality and operational efficiency.
As the landscape of manufacturing evolves, the importance of die casting continues to grow, showcasing the remarkable capabilities of this technique in producing reliable and complex components. By partnering with experienced manufacturers, businesses can leverage die casting's benefits and achieve a competitive edge in their respective industries.
At Deep Mould, we are committed to delivering top-quality die casting services. Our expertise in metal fabrication, combined with advanced technology and a dedication to excellence, positions us as leaders in the field. Explore how we can meet your manufacturing needs with our comprehensive solutions in die casting.